問題
III – 8 大型モータの組立作業を2名の作業者と1台のホイスト(荷役装置)を用いて協同して作業を行っている。
この作業は稼働率が低く、作業者の待ち時間及びホイストの待ち時間の削減を目標とする場合、次の手法のうち、現状分析を行うときに最も適切なものはどれか。
① 連合作業分析
② 製品工程分析
③ ストップウォッチ法
④ サーブリッグ分析
⑤ ワークサンプリング
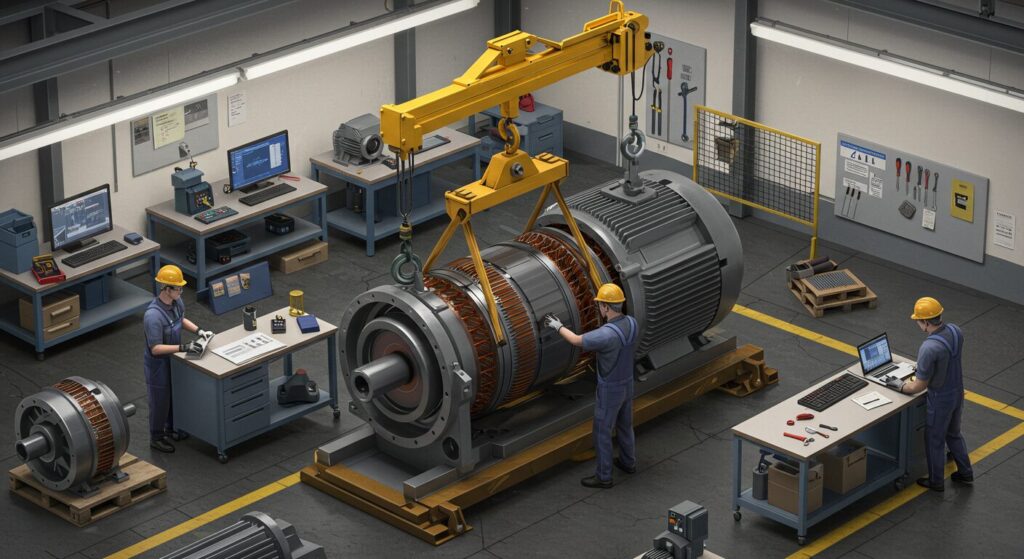
解答
正解は 1 になります。
問題の概要解説
この問題は、経営工学における「現状分析」の手法を問うものです。特に、大型モータの組立作業という具体的な作業環境において、作業者とホイスト(荷役装置)の稼働率が低いという課題があります。この状況を改善するために、まず現状を正確に把握する必要があります。その際、どの分析手法が最も適しているかを選ぶ問題です。
キーワードの整理
- 稼働率が低い:作業者や設備が十分に活用されていない状態。
- 待ち時間の削減:作業者やホイストが無駄に待機する時間を減らすこと。
- 現状分析:問題を解決するために、まず現在の状況をデータとして把握すること。
このような状況では、作業者とホイストの動きや稼働状態を詳細に観察・記録し、どこに無駄や非効率があるかを明らかにする必要があります。
各選択肢の詳細解説
① 連合作業分析
連合作業分析は、複数の作業者や設備が協力して行う作業を対象とした分析手法です。具体的には、各作業者や設備がどのタイミングで何をしているかを時間軸で記録し、相互の関係性や効率性を評価します。
- 適用例:今回のように「2名の作業者」と「1台のホイスト」が協同して作業する場面で有効です。
- メリット:個々の動きだけでなく、全体の調和(協調性)を見ることができる。
- 今回との関連性:まさにこの問題の状況(協同作業)にピッタリ合致します。
→ 正解はこれです。
② 製品工程分析
製品工程分析は、製品が完成するまでの工程全体を記録・分析する手法です。主に製造プロセス全体を対象としており、「どこでどれくらい時間がかかっているか」や「どの工程で無駄が発生しているか」を調べます。
- 適用例:製品全体の流れを見る場合(例:原材料から完成品まで)。
- メリット:工程全体のボトルネック(遅延要因)を特定できる。
- 今回との関連性:今回の問題は「特定の作業」に焦点を当てており、この手法では範囲が広すぎます。
→ 不適切です。
③ ストップウォッチ法
ストップウォッチ法は、その名の通りストップウォッチを使って作業時間を測定し、効率性や標準時間を評価する手法です。個々の動作や工程ごとの時間計測に適しています。
- 適用例:単純な繰り返し作業や個人作業。
- メリット:細かい動作ごとの正確な時間データが得られる。
- 今回との関連性:協同作業全体ではなく、個別動作に特化しているため範囲が狭すぎます。
→ 不適切です。
④ サーブリッグ分析
サーブリッグ分析は、人間工学的な視点から作業動作そのものを細分化し、「無駄な動き」を排除するための手法です。「つかむ」「持つ」「移動する」など基本動作レベルで評価します。
- 適用例:単純な反復作業や動きそのものに焦点を当てる場合。
- メリット:細かな動きまで徹底的に分析可能。
- 今回との関連性:協同作業全体ではなく、個々人の動きだけを見るため不十分です。
→ 不適切です。
⑤ ワークサンプリング
ワークサンプリングは、一定間隔でランダムに観察し、その時点で何が行われているかを記録する手法です。これによって稼働率や非稼働率(待機時間など)を推定します。
- 適用例:大規模な工場や長期間観察が必要な場合。
- メリット:大まかな傾向を見るには有効。
- 今回との関連性:詳細なタイミングや相互関係を見るには不十分です。
→ 不適切です。
まとめ
この問題では、「2名の作業者と1台のホイスト」という協同作業環境で稼働率向上を目指すため、現状分析として最も適切な手法を選ぶ必要があります。それぞれの選択肢について検討した結果、
- 正解は①「連合作業分析」です。この手法は複数人・複数設備が協力して行う作業全体を可視化し、待ち時間や非効率部分を特定するために最も適しています。
問題要点
- 協同作業環境では「連合作業分析」が有効。
- 他手法(製品工程分析・ストップウォッチ法・サーブリッグ分析・ワークサンプリング)は範囲や目的が異なるため不適切。
感想
このあたり、過去にもたくさん出てきています。
リンクを貼るより、タグクラウドを見ていただいた方が早いのですが。
タグクラウドももう少し使いやすくなるよう整備しなくちゃ・・・。
今年はこのへんの業務も行えるかもしれない!
やっぱり実務での経験はまったく違う物ですからね。
このブログの説得度も倍増するはず!
ご期待下さい。